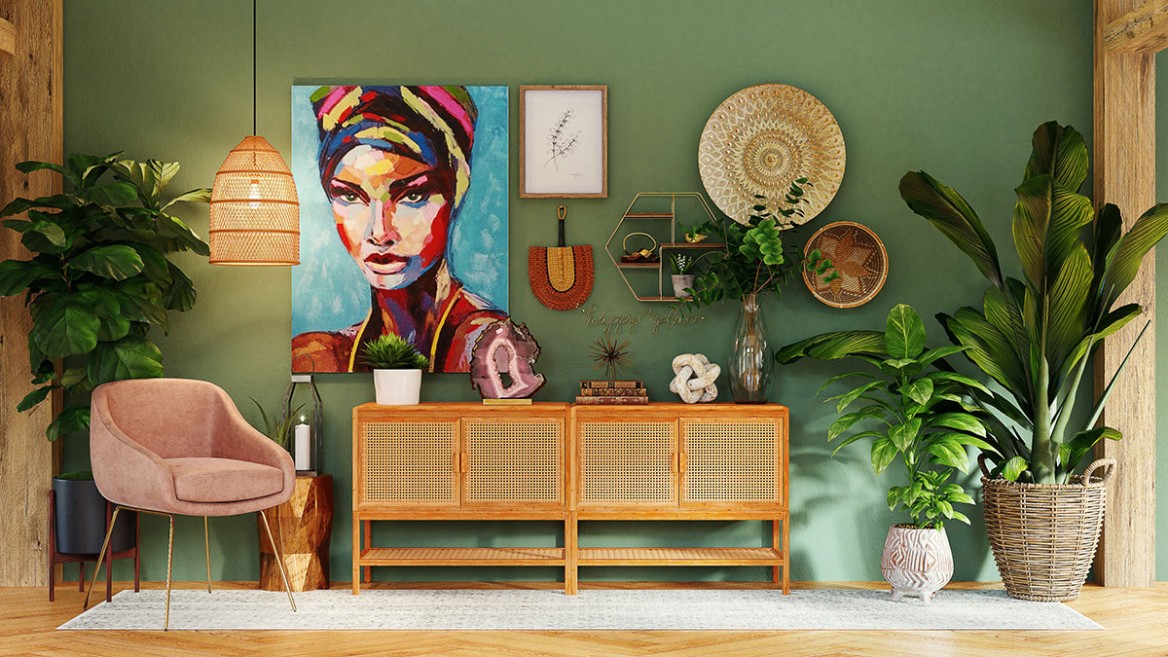
Koelnmesse - Competence for the furniture industry
Thank you for your interest in Koelnmesse's digital products and services. As we are always developing digital products for our individual trade fair brands, the ambista platform as a B2B network for the international furnishing industry will no longer be operated as of 30.11.2022. As a registered ambista user, we have already informed you about the shutdown of ambista on November 9, 2022. If you still have questions, please feel free to contact us .
Here you will find more detailed and in-depth content as well as information on the individual branches:
The categories of the imm cologne magazine